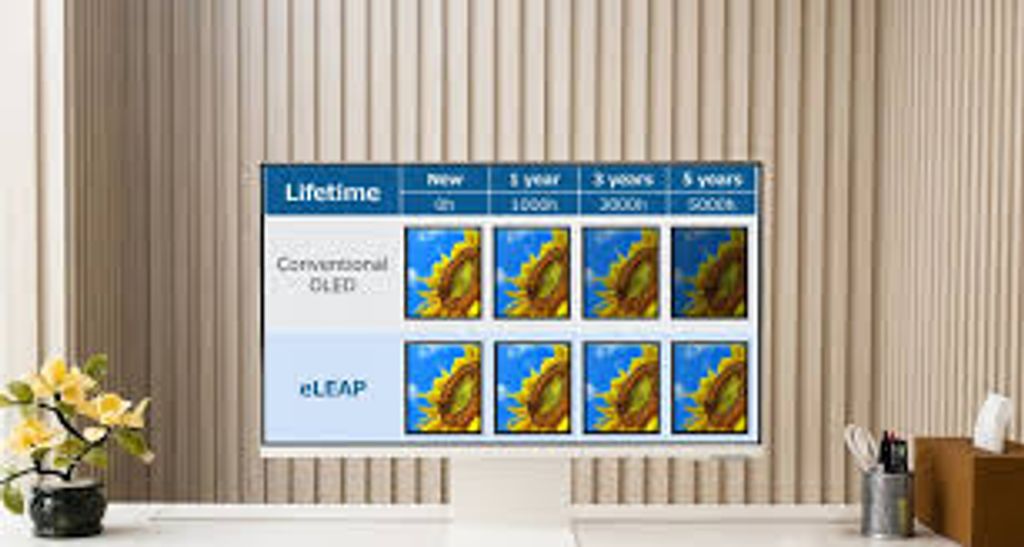
LG Display is investing almost a billion dollars in a new generation of OLEDs, and in addition to the previously discussed technologies, the company intends to take a closer look at production using the "eLEAP" technology.
The eLEAP technology, developed by Japan Display Inc. (JDI), stands for: environment positive, Lithography with maskless deposition, Extreme long life, low power, and high luminance, Any shape Patterning.
In simpler terms, eLEAP enables the deposition of OLED material without the use of fine metal masks (FMM). This allows for a significantly higher opening ratio (60% compared to around 30%), which translates to double the efficiency, double the peak brightness, and even three times the lifespan. When using a tandem structure, this technology can achieve brightness exceeding 3000 nits.
LG Display considers eLEAP
The eLEAP technology has been developed over the years. Although Japan Display started small-scale production at the end of 2024, eLEAP panels have not yet appeared in popular consumer products. The company is actively seeking a partner to help scale up production.
According to reports from the Korean newspaper The Elec, LG Display is now planning to test eLEAP technology in RGB OLED panels at its existing E4 factory in Paju, South Korea.
LG Display is reportedly able to utilise its current production lines after implementing certain modifications. However, the company is not yet ready for a full investment – initially, the technology would be used in niche OLED panels with a diagonal size of 20–30 inches.
Not just LG Display
Although Japan Display is the main initiator of eLEAP, other companies are also involved in the project.
At the end of 2024, reports emerged about a connection with the new production platform "Max OLED" from Applied Materials, which Samsung Display plans to use for creating enhanced RGB OLED panels for smartphones, tablets, laptops, monitors, and possibly even televisions.
The Chinese company Visionox is also developing its own version of maskless OLED production called "ViP," using production machines from Applied Materials.
Source: flatpanelshd.com